不同工艺和原料路线生产烯烃的碳排放强度及结构
《化学工业》2022年第1期 / 2022-03-31 17:19:30
根据中国碳核算数据库(CEADs)数据,根据终端能源消费量核算,2019年我国表观CO2排放量104.34亿t[1]。根据我国能源消费数据测算,2020年我国表观CO2排放量约105亿t。2020年石化化工行业CO2排放量约14.8亿t(含外购热力、电力带来的间接排放)。2020年,我国以烯烃为主要目标产品的生产工艺蒸汽裂解、煤/甲醇制烯烃、丙烷脱烃等(不考虑炼厂副产丙烯),不同的烯烃生产工艺路线的碳排放特点差异较大。
蒸汽裂解装置是在高温和水蒸汽存在的条件下发生分子断裂和脱氢反应生产烯烃,目前主流蒸汽裂解装置单位烯烃(乙烯+丙烯)燃动能耗在400~430 kgoe/t烯烃。蒸汽裂解制烯烃主要的CO2排放来自裂解炉燃料气燃烧,约占整个生产过程碳排放的80%以上,少部分来自驱动各种压缩机所需的蒸汽和电力带来的碳排放,约占15%~20%,工业生产过程排放较少,主要是烧焦产生的部分CO2排放,约占总排放量的1%。装置规模是影响蒸汽裂解碳排放强度的重要因素,装置规模越大,裂解和分离过程效率越高,吨烯烃排放强度越低。百万吨级以上的大型裂解装置吨烯烃排放强度约为30万吨级小裂解装置的2/3。综合计算,百万吨级规模石脑油蒸汽裂解装置CO2排放强度约为1t CO2/t烯烃(乙烯+丙烯)。若采用液化气、乙烷等轻质原料,CO2排放强度可达到0.8t CO2/t烯烃(乙烯+丙烯)以下。
丙烷脱氢以丙烷为原料,在催化剂作用下发生脱氢反应生产丙烯。当前主流丙烷脱氢装置燃动能耗在400~500 kgoe/t丙烯,略高大规模蒸汽裂解装置吨烯烃能耗,其中Lummus公司的Catofin固定床工艺能耗低于UOP公司的Oleflex移动床工艺[2]。丙烷脱氢装置的主要能耗来自驱动压缩机所需的蒸汽,以及加热炉所需的燃料气。根据规模和工艺技术的不同,吨烯烃CO2排放量约为1.2~1.4t,单位产品排放强度高于大规模的蒸汽裂解装置。
煤/甲醇制烯烃的CO2排放可分为两个环节,即煤制甲醇和甲醇制烯烃。其中,煤制甲醇环节是CO2排放的主要来源。由于煤炭原料氢碳比低,煤气化合成气不能满足甲醇合成氢碳比2.0的要求,需要通过水煤气变换将CO转化为CO2并生成氢气,以满足甲醇合成要求的碳氢比,这一过程产生大量的CO2排放。另外,大型煤气化装置一般采用纯氧氧化,需要大规模的空分装置和锅炉驱动,燃料煤燃烧也产生大量CO2排放。目前主流工艺吨甲醇CO2排放约为3t。甲醇制烯烃(MTO)过程的主要能耗来自蒸汽和电力,吨烯烃排放约为1.3t CO2(乙烯+丙烯)。综合煤制甲醇环节和甲醇制烯烃环节,煤制烯烃(CTO)吨烯烃排放约为10t CO2(乙烯+丙烯)左右。
不同工艺和原料路线生产烯烃的碳排放强度及结构如图1所示。

免责声明: 1. 本文转自网络/其他媒体,转载目的在于传递更多信息供参考,非商业用途。 2.. 本文仅代表原作者观点,与[经济形势报告网]无关。内容真实性、准确性未经核实,读者据此操作风险自担。 3. 如涉及版权问题,请权利人第一时间通过[邮箱/电话]联系我们,我们将立即删除。 4. 转载时禁止篡改内容或用于违法用途。5. 本声明最终解释权归[经济形势报告网]所有。
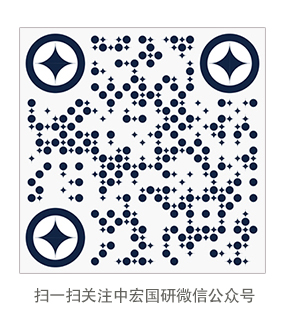
1.本站遵循行业规范,任何转载的稿件都会明确标注作者和来源;
2.本站的原创文章,请转载时务必注明文章作者和"来源",不尊重原创的行为本站或将追究责任;
最新新闻
热点文章
热点标签
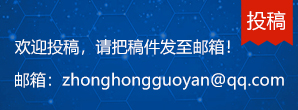